BY TIM PENNINGTON, EDITOR-IN-CHIEF | 08 MARCH 2024
In the middle of a cold winter, the workers at Tri-State Fabricators near Cincinnati can only think of the warm sun.
That’s because the sun’s solar power gives the energy needed to a unique product that the manufacturer helps produce for one of its clients, and a durable powder coat is used to help finish it, too.
Tri-State Fabricators helps manufacture what are called “aesthetic solar structures” made by Spotlight Solar in North Carolina, which are shaded sitting areas —tables and benches — that have a canopy overtop of them that has solar panels to collect energy and provide it to the people sitting in the area.
125,000 SF Facility Includes Fabrication, Welding, Finishing
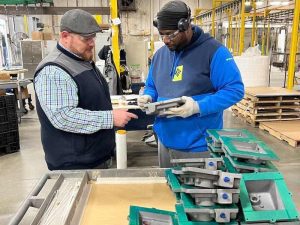
“We manufacture the parts for them, weld them all together, and put a wet coat or a powder coat on them to finish them off,” says Josh Johnson, Operations Manager at Tri-State Fabricators, who oversees all the processes inside the 125,000 square feet facility just east of Cincinnati.
“There are a few processes such as wiring that we need to send out to have completed, but we put it all together and get them shipped out to their customers,” Johnson says.
Tri-State Fabricators has been helping Spotlight Solar build the systems since 2016. Craig Merrigan, Spotlight Solar’s Co-Founder and CEO, formed the company with Co-Founder Rob Surra in 2010 to market a product to companies and institutions that wanted to show they supported clean energy customers, such as universities and large institutions.
“We decided that there ought to be a way to make solar highly visible, highly engaging, and beautiful to capitalize on that affinity that people have for it,” Merrigan said in 2019. “And the effect of that is to increase adoption by making it a lot more visible.”
Show Environmental Care and Clean Energy Adoption
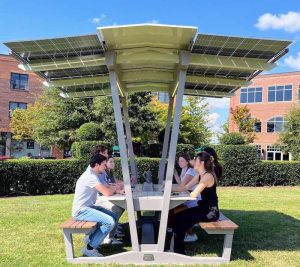
Merrigan says Spotlight Solar had three goals when it launched: helping property owners show environmental care, creating dignifying work, and increasing the adoption of clean energy.
“People love solar technology, but since it accounts for less than 3% of our electrical generation and hides on flat rooftops,” he says. “We rarely see it. It needs visibility for purchase consideration to increase.”
Spotlight Solar calls that awareness a “return on visibility” and cites a study from Yale that shows that visibility is a highly important factor in accelerating the adoption of solar.
One of the products the company has Tri-State Fabricators make for them is called the “Haven,” a seating area where visitors can not only sit and relax but also use the electricity from the solar panels to power their devices like computers and phones.
The Haven sells particularly well for schools, universities, and large corporate campuses.
“People want to be outside, whether they’re working, eating or hanging out,” Merrigan says. “So, they need space, shade, and shelter. And they need power.”
From Subcontractor to Manufacturing Partner
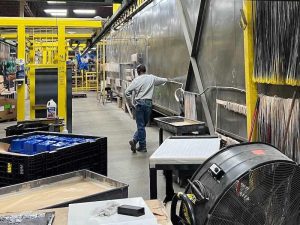
Because Tri-State Fabricators has a manufacturing process with welders, fabricators, and a finishing system, they were a perfect match for Spotlight Solar to partner with them on building these structures.
Originally, Tri-State Fabricators was a subcontractor for a project that performed welding and coating. However, they eventually began working directly with Spotlight Solar as their main component supplier.
Tri-State Fabricators was started in 1983 by Jay Richard Vogt and his three sons, Rick, Jeff, and Chris. The Vogts say the company began with one overarching goal: to create a metal fabrication company that profoundly cared about creating long-term partnerships with its customers, employees, suppliers, and community.
Their original location was an old milk factory closer to downtown Cincinnati. Still, as their customer base grew, they needed to add more services and space to their operation.
Tri-State Fabricators eventually found 20 acres of land to build a custom facility to house their various departments: engineering, fabrication, welding, paint and powder coating, and assembly.
Premier Contract Manufacturers in the Midwest
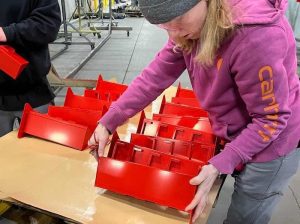
The company soon became one of the premier contract manufacturers in the Midwest, and its paint and powder coating line has played a huge role in that growth.
Tri-State Fabricators added a finishing line to help become a full-service provider for their customers, including wet paint and powder coating operations.
“We did an upgrade of our powder coating line in 2021 to give two people the ability to spray, and they are offset from each other,” Johnson says.
The system includes a full conveyor system for handling many parts, and for larger-sized parts — or smaller quantity runs — they have two independent powder coat booths and ovens.
Tri-State Fabricators also runs a full-service conveyor line for painting when the project doesn’t specify powder coating. When the parts get big and heavy, they roll out their custom paint racks and oversize booths to finish products. Utilizing their partnerships with all the major paint brands, they can match virtually any color with wet paint.
Ability to Apply Chemical Agent Resistant Coatings
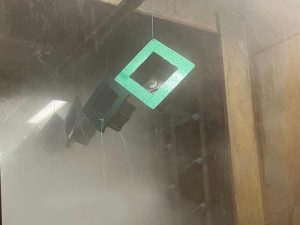
The company is also certified to apply chemical agent-resistant coatings (CARC), a paint commonly applied to military vehicles to provide protection against chemical and biological weapons.
“We have not had a big demand for CARC,” Johnson says. “But it is something that we want to increase where we can.”
Tri-State Fabricators utilizes a zinc phosphate wash to clean and etch the material to ensure the best paint adhesion possible. The unique design of our 3-stage wash system does the work like a 5-stage system.
The facility also has a large area to use abrasive media blasting, which they say is an excellent way to remove old paint and rust and increase the paint or powder adhesion. Johnson says the glass beads produce a much smoother and brighter finish than angular abrasives, leaving the part clean without any dimensional change. Chemically inert and environmentally friendly, Johnson says they can recycle their beads approximately 30 times, making them a more preferred method of metal cleaning or surface finishing.
“That’s one of the things that separates us from some of our local competition around here,” Johnson says. “We have a large sandblasting and powder coating booth, so we can do some rather large parts that you can’t necessarily do on a line. Some of our competitors only have lines, but we can do very large structures.”
Johnson says the Spotlight Solar company likes the powder coating because of its ultraviolet protection and durability, but some of their other customers still like to have the flexibility that wet paint provides, especially in matching colors.
Adding ‘Dual-Line’ Coating Process in 2025

Tri-State Fabricators is now getting quotes and engineering a new dual-coat finishing line that can handle wet paint or powder coating. Johnson says they hope to get the line in place in 2024 or early 2025, giving them more flexibility on either wet or powder processes.
“We want to get out of doing the wet paint, but at the same time, we are staying in it,” he says. “It takes a little more of a higher skill set for a paint to coat in wet paint than powder, and we want to make it easier to find the right people when we need them.”
Currently, only 25% of their customers are requesting wet paint applications, and that number may dwindle even further. The new dual-line will give Tri-State Fabricators the ability to have a second powder coating line when needed while still having wet paint application ability.
“It gives us more capabilities to run two lines,” Johnson says. “Sometimes you need to wash a part before you can wet coat them, and we have to shut down the powder coating line if we’re running parts on the washer, which means we are not getting product out. If we have the dual coat line, we can run those parts on that line through the washer, turn them around, and wet coat them.”
That scenario comes into play when a customer requests a zinc primer with a powder coating. Johnson says they can wet coat over primer — or can wet coat over powder — but you can’t powder coat over wet coat.
Speeding Up Process and Providing Coating Protection
“We like to speed up the process, and it does have better protection over the long run because the powder is good at corrosion protection,” he says. “We like to do a zinc prime powder coat and then turn it around and put a wet coat top base top coat to make it even more protective.”
In the meantime, Tri-State Fabricators will continue working with companies like Spotlight Solar on building and coating their products, especially with a capable coating operation like the one they have, adding wet paint and powder coating.
And when the new dual line comes together in 2025, Johnson thinks they will raise the bar on speed and quality even more. He says his coating team is performing better than he has ever seen.
“We’ve got the current line humming so well for the most part,” he says. “The paint line doesn’t become too much of a choke point with too much coming over at once. That can always happen, but they are so good that when we ramp up fully staffed, they are some of the best power coaters around.”